
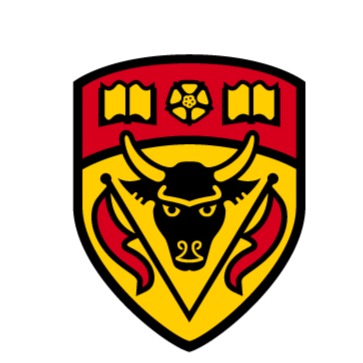
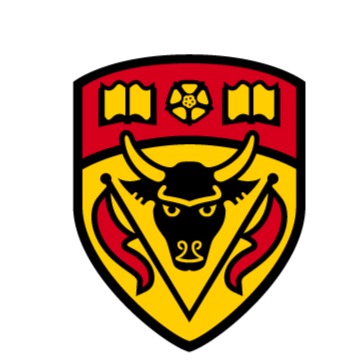
- Location
- Calgary, Alberta, Canada
- Companies
-
-
Calgary, Alberta, Canada
-
- Categories
- Supply chain optimization Operations Machine learning Data science Scientific research
Achievements
Latest feedback
Recent projects
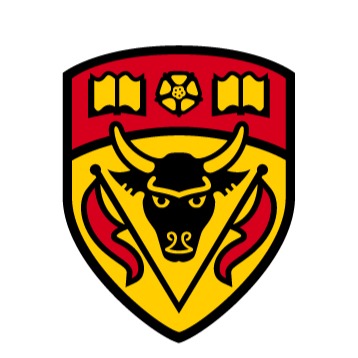
Material Tracking for Production Processes
In this project, the inventory tracking and materials flow process that starts from the receipt of goods from the warehouse till the end of the production run as a labeled batch will be analyzed. The issues and the root causes of the problems mentioned above need to be identified. Recommendations to improve the process should be developed along with detailed process charts and procedures. The main cause of the problems identified should be tackled by recommending an improved inventory and material tracking process that reduces or eliminates any discrepancies.. Key Considerations: · Production volumes vary throughout the year. In the summer months, minimum production occurs.· Bulk drums are repackaged into smaller containers. The label on these drums is different from the label attached to the repackaged drum. · There is a warehouse located close to this production site that is used to store inventory. Multiple transfers occur between the two sites on a daily basis for materials as needed for production.
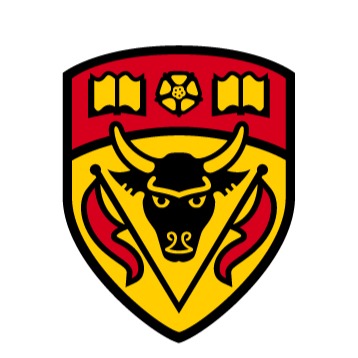
Pick Belt Capacity Optimization Project
Frito Lay Western Canada (PepsiCo Foods Canada) has two Alberta manufacturing facilities that are located 45 minutes apart. The Lethbridge facility produces corn-based products and operates as the hub for warehousing and distribution. The Taber facility produces potato-based products and directly ships finished goods to Lethbridge for warehousing and distribution.Due to business growth in the last three years, the Lethbridge warehouse has run out of capacity on the pick belt (full case picking) resulting in more walk back locations and less efficient order picking.The main goal of this project is to analyze the performance of PepsiCo’s pick belt from a product allocation perspective and identify what and when they should store on the pick belt. By the end of this project, it is expected to have developed a mathematical model that determines the optimal product allocation and scheduling of the pick belt, along with recommendations on other suitable solutions to support business growth.